Food Beverages
Description:
Filter Press are pressure filter in which a filter package formed by filter plates and filter frames or chamber plates is installed in a stand between a “fixed cover” and a “loose cover”.
There elements are plane- parallel to each other and are pressed together by the fixed cover and the loose cover.
The fixed cover is connected to the traverse via connecting and tie bars. Together they form the
press stand. The filter package is pressed together by the a pressure unit which is incorporated in the traverse and acts on the loose cover.
Between the individual filter plates or chamber plates there are filter cloths which have an outward sealing function under the pressure applied. The unfiltrate is conveyed into the chambers via a pump.
The filtrate passes through the filter medium, leaves the filter via internal or external outlet channels and is conveyed further according to its intended usage.
Filtration produces a filter cake, which can be washed if required.
In the membrance filter press every second plates is equipped with an inflatable membrance. After the end of the filtration process the membrance plates are pressurized with compressed air or water and forced against the cake. The cake is thus also drained mechanically and the process accelerated.
Benefits from the use of membrance plates:
- Higher yield, virtually no loss.
- Drier filter cake
- Filtration cycle shortened by appro.50%
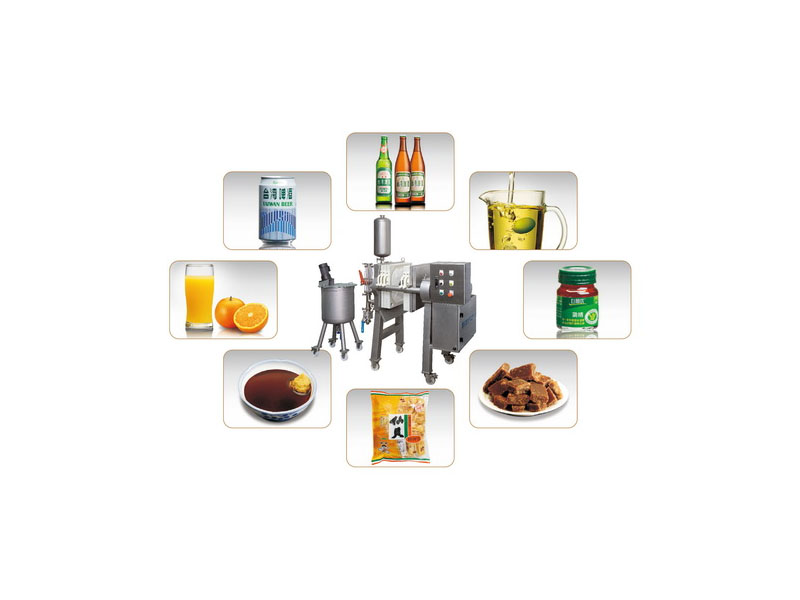
Description:
Filter Press are pressure filter in which a filter package formed by filter plates and filter frames or chamber plates is installed in a stand between a “fixed cover” and a “loose cover”.
There elements are plane- parallel to each other and are pressed together by the fixed cover and the loose cover.
The fixed cover is connected to the traverse via connecting and tie bars. Together they form the
press stand. The filter package is pressed together by the a pressure unit which is incorporated in the traverse and acts on the loose cover.
Between the individual filter plates or chamber plates there are filter cloths which have an outward sealing function under the pressure applied. The unfiltrate is conveyed into the chambers via a pump.
The filtrate passes through the filter medium, leaves the filter via internal or external outlet channels and is conveyed further according to its intended usage.
Filtration produces a filter cake, which can be washed if required.
In the membrance filter press every second plates is equipped with an inflatable membrance. After the end of the filtration process the membrance plates are pressurized with compressed air or water and forced against the cake. The cake is thus also drained mechanically and the process accelerated.
Benefits from the use of membrance plates:
- Higher yield, virtually no loss.
- Drier filter cake
- Filtration cycle shortened by appro.50%
Materials
The filter stand is made of nonrust stainless steel; painted steel is also available.
The filter plates are of polypropylene although other materials are also possible as required. The filter cloths are generally also made of polypropylene.
Application and options for use
Filter presses are used in all branches: foodstuffs and drinks, chemistry, pharmaceutical or in the environmental sector.
Filtration with filter aids
As filter aids kieselguhr or perlite are generally added to facilitate filtration.
Precoating
Before the star of actual filtration the filter cloth is coated with a layer of the filter aid. This prevents bleeding and protects the filter cloth from blockage. We recommend the doing unit for precoating and subsequent metered addition of the filter aid to ensure optimum mixing and dosing of necessary quantity of filter aids.
Clean System type
A hermetically sealed filter can be achieved using filter plates equipped with an O-ring rim seal.
The filter cloths have an all-round sealing bead and are attached within the plate.
The patented sealing bead is bead is designed so that no soiling can get behind the sealing bead. Filters remain clean and aseptic on the outside.
Drainage of solid matter/Sludge drainage
In the case of products with a high solid matter content this is retained in the chambers of the filter until solid cake has formed.
Washing and drying of filter cake
Substances to be recovered or removed can be washed out from the previously drained solid matter by adding certain solvents. The plates and frames used for this purpose are equipped with special washing channels. The filter cake can be additionally dehydrated using membrance plates followed by compressed air blown through the filter cake.
- The filter plates and filter clothes are made of high-pressure- and heat-resistant materials.
- A hygienic-class connector is used.